Grinding discs play a pivotal role in various industries, facilitating the shaping and finishing of materials. However, like any other tool, they are not immune to issues that can hamper their efficiency and performance. In this article, we'll delve into common grinding disc issues, explore their root causes, and provide effective solutions for a seamless workflow.
Introduction
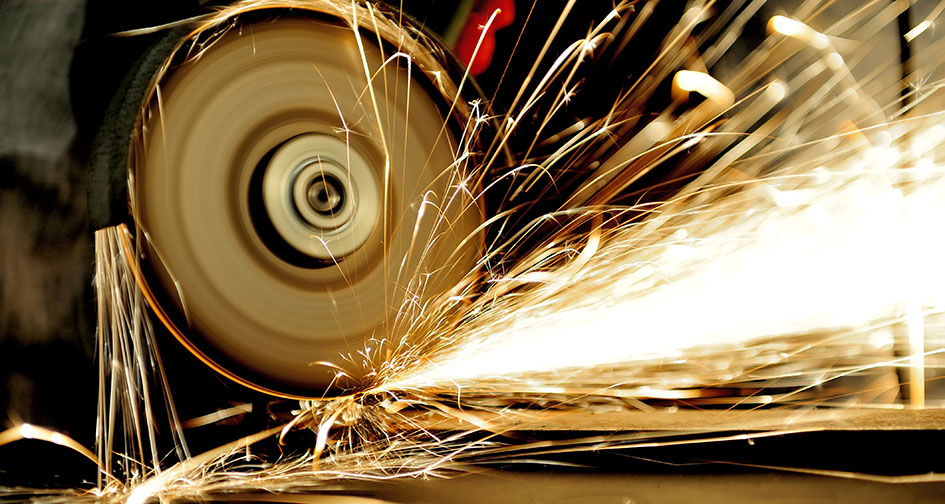
Grinding Discs play a fundamental role in various industries, serving as essential tools for material removal, shaping, and finishing processes. Understanding their definition, importance across industries, and common issues faced is crucial for optimizing their use and ensuring efficient operations.
A. Definition of Grinding Discs
Grinding discs are abrasive tools used in machining processes to cut, grind, or polish surfaces of materials. These discs typically consist of abrasive particles bonded to a backing material, creating a rotating tool that can remove excess material, smooth surfaces, or sharpen edges. They come in various shapes and sizes, each designed for specific applications.
B. Importance in Various Industries
Metalworking Industry:
In metal fabrication and manufacturing, grinding discs are vital for shaping, deburring, and finishing metal surfaces. They are commonly used with angle grinders to achieve precise dimensions and surface quality.
Construction Industry:
Construction professionals rely on grinding discs for tasks such as concrete surface preparation, smoothing rough edges, and removing imperfections in materials like stone and concrete.
Automotive Industry:
Grinding discs are essential in the automotive sector for tasks ranging from sharpening tools to shaping and finishing metal components. They contribute to the precision and quality of automotive parts.
Woodworking Industry:
Woodworkers utilize grinding discs for shaping and smoothing wooden surfaces. These discs are effective in removing excess material, refining shapes, and preparing wood for further finishing.
General Manufacturing:
Grinding discs find applications in various manufacturing processes where precise material removal is required, contributing to the production of high-quality components.
C. Common Issues Faced
Disc Wear and Abrasion:
Continuous use can lead to wear and abrasion of the grinding disc, affecting its performance. Regular inspection and replacement are necessary to maintain efficiency.
Overheating:
Excessive friction during prolonged use may lead to overheating, affecting the disc's durability and the quality of the finished surface. Proper cooling measures and periodic breaks are essential.
Clogging:
Grinding discs can accumulate material residues, reducing their effectiveness. Regular cleaning or choosing discs with anti-clogging features helps prevent this issue.
Vibration and Wobbling:
Imbalances or uneven wear may result in vibration or wobbling, impacting both the quality of the finish and the safety of the operation. Proper installation and balancing are critical.
Incorrect Disc Selection:
Choosing the wrong type of grinding disc for a specific material or application can lead to inefficiency and potential damage. Proper selection based on material compatibility is essential.
Understanding the definition, significance, and potential challenges associated with grinding discs is essential for industries relying on these tools. By addressing common issues and ensuring proper usage, industries can maximize the effectiveness of grinding discs in their respective applications.
Wear and Tear on Grinding Discs
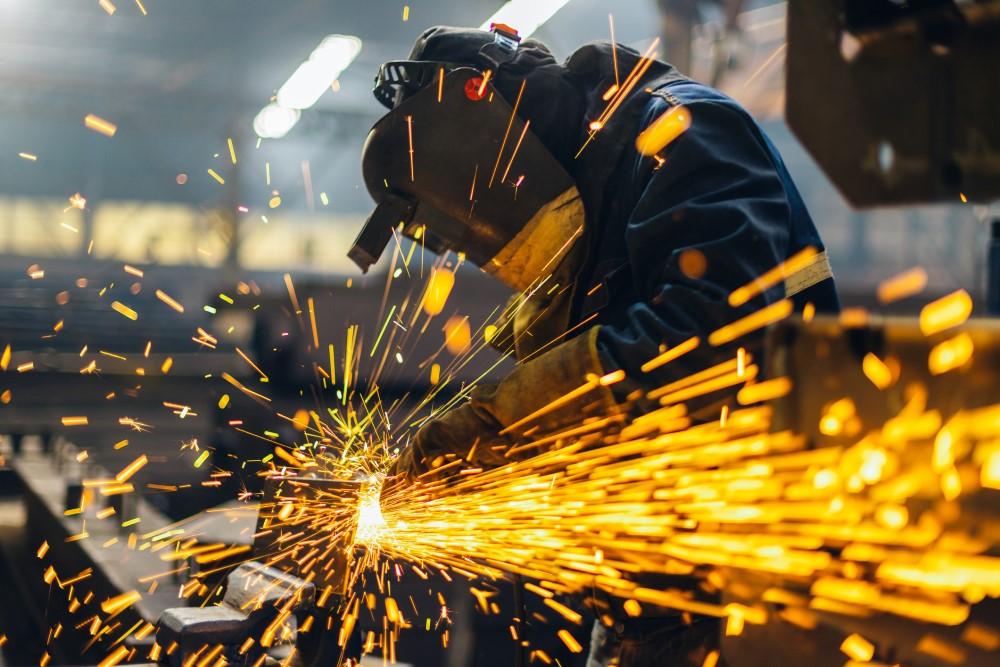
Grinding discs are essential tools in various industries, providing the necessary abrasion for tasks ranging from metal fabrication to concrete polishing. Understanding the factors contributing to wear and tear on grinding discs is crucial for optimizing their performance and ensuring safety.
Material Hardness and Composition:
Hardness Variation: Grinding discs encounter materials with varying hardness levels. Abrasive materials like metal and concrete can differ significantly in hardness. Continuous grinding against hard materials accelerates wear.
Material Composition: The presence of abrasive elements in the material being ground can impact the wear on the grinding disc. Abrasive particles can accelerate the wearing down of the disc.
Grinding Pressure and Force:
Excessive Pressure: Applying excessive pressure on the grinding disc can lead to quicker wear. It's essential to use the recommended pressure for the specific application to avoid unnecessary strain on the disc.
Inadequate Force: On the other hand, insufficient force may result in prolonged grinding, generating additional friction and heat, contributing to wear.
Disc Quality and Composition:
Quality of Abrasive Material: The quality of the abrasive material used in the grinding disc significantly influences its lifespan. High-quality abrasive materials tend to resist wear and maintain sharpness longer.
Bonding Agent: The bonding agent that holds the abrasive particles together plays a crucial role. A well-designed bonding agent enhances the disc's durability.
Work Environment Conditions:
Temperature: Elevated temperatures generated during grinding can impact the disc's composition. Excessive heat weakens the bonding agent and accelerates wear.
Moisture and Contaminants: Exposure to moisture or contaminants in the work environment can affect the grinding disc's integrity, leading to faster wear.
Operator Technique:
Proper Technique: Operator skill and technique are vital. Improper use, such as grinding at incorrect angles or using excessive force, can contribute to uneven wear and reduce disc longevity.
Regular Inspections: Operators should regularly inspect the grinding disc for any signs of damage or wear. Discs showing wear beyond a certain point should be replaced promptly.
Disc Size and RPM Compatibility:
Correct Sizing: Using the correct disc size for the grinder is crucial. Incorrectly sized discs may wear unevenly or pose safety risks.
RPM Compatibility: Adhering to the recommended revolutions per minute (RPM) for the grinding disc ensures optimal performance and prevents premature wear.
Regular maintenance, adherence to recommended operating conditions, and selecting the right grinding disc for the task are essential practices to minimize wear and tear. By understanding the factors influencing wear, operators can enhance the longevity and efficiency of grinding discs, contributing to safer and more productive grinding operations.
Uneven Grinding
Uneven grinding refers to the situation where the surface being ground does not achieve a consistent and smooth finish. This issue can arise for various reasons and can impact the quality of the workpiece. Here are common factors contributing to uneven grinding and potential solutions:
Incorrect Grinding Wheel Selection:
Solution: Ensure that the grinding wheel is suitable for the material being ground. Different materials require specific abrasive properties. Choose the right wheel type, grit size, and bond for the application.
Improper Wheel Dressing:
Cause: A grinding wheel that is not properly dressed can lead to uneven wear and ineffective cutting.
Solution: Regularly dress the grinding wheel to maintain its shape and remove any accumulated debris. Proper dressing ensures a consistent cutting surface.
Inadequate Grinding Fluid or Coolant:
Cause: Insufficient or improper use of grinding fluid can result in increased friction and heat, leading to uneven grinding.
Solution: Use an appropriate grinding fluid or coolant to dissipate heat and reduce friction. Proper cooling is essential for achieving uniform results.
Incorrect Grinding Parameters:
Cause: Using incorrect grinding parameters such as excessive speed, feed rate, or depth of cut can lead to uneven grinding.
Solution: Adjust the grinding parameters according to the material and application requirements. Refer to manufacturer recommendations for optimal settings.
Worn Grinding Wheel:
Cause: A worn-out grinding wheel may not provide a consistent cutting surface, resulting in uneven grinding.
Solution: Replace the grinding wheel when it reaches the end of its usable life. Regularly inspect the wheel for signs of wear.
Uneven Pressure or Feed Rate:
Cause: Uneven pressure or inconsistent feed rates during grinding can lead to irregular material removal.
Solution: Apply uniform pressure and maintain a consistent feed rate across the workpiece. Operator skill and attention to detail are critical.
Machine Issues:
Cause: Mechanical problems with the grinding machine, such as misalignment or issues with the spindle, can result in uneven grinding.
Solution: Conduct regular maintenance checks on the grinding machine. Address any mechanical issues promptly to ensure proper functionality.
Workpiece Fixturing:
Cause: Poorly secured or misaligned workpieces can lead to uneven grinding.
Solution: Ensure proper fixturing and alignment of the workpiece. Secure it tightly to prevent movement during the grinding process.
Addressing uneven grinding requires a combination of proper equipment setup, correct operating parameters, and regular maintenance practices. Operators should be trained to identify and rectify issues promptly to achieve high-quality and consistent results in grinding applications. Regular inspections and adherence to best practices contribute to efficient and uniform material removal during the grinding process.
Overheating Problems
Overheating during grinding is a common issue that can affect the performance of both the grinding wheel and the workpiece. Excessive heat can lead to various problems, including reduced wheel life, thermal damage to the workpiece, and overall diminished grinding efficiency. Here are potential causes and solutions for addressing overheating problems:
Incorrect Grinding Parameters:
Cause: Using improper grinding parameters, such as excessive speed, feed rate, or depth of cut, can generate excess heat.
Solution: Adjust the grinding parameters within the recommended range. Consult the manufacturer's guidelines for optimal settings based on the material being ground.
Inadequate Cooling or Lubrication:
Cause: Insufficient use of coolant or grinding fluid can result in increased friction and heat.
Solution: Ensure an adequate supply of coolant or lubricant during the grinding process. Proper cooling helps dissipate heat and prevents thermal damage.
Incorrect Wheel Selection:
Cause: Choosing a grinding wheel with inappropriate specifications for the material being ground can lead to overheating.
Solution: Select a grinding wheel with the correct abrasive type, grit size, and bond for the specific application. Matching the wheel to the material minimizes heat generation.
Workpiece Material Issues:
Cause: Some materials, especially those with poor thermal conductivity, are more prone to overheating during grinding.
Solution: Adjust grinding parameters for materials with lower thermal conductivity. Consider using a specialized grinding wheel designed for heat-sensitive materials.
Wheel Dressing Problems:
Cause: Irregularities or improper dressing of the grinding wheel can lead to uneven contact and heat buildup.
Solution: Regularly dress the grinding wheel to maintain its shape and remove any glazing or accumulated debris. Properly dressed wheels ensure consistent grinding performance.
Inadequate Machine Maintenance:
Cause: Poorly maintained grinding machines can contribute to overheating issues.
Solution: Conduct regular maintenance on the grinding machine, including checking coolant systems, inspecting wheel dressing equipment, and ensuring proper alignment. Address any mechanical issues promptly.
Insufficient Wheel Coolant Flow:
Cause: Inadequate coolant flow to the grinding zone can result in reduced heat dissipation.
Solution: Check and optimize the coolant delivery system. Ensure that the coolant effectively reaches the grinding zone to maintain cooling efficiency.
Excessive Grinding Time:
Cause: Prolonged grinding sessions without breaks can contribute to heat buildup.
Solution: Implement intermittent grinding and allow breaks to prevent excessive heat accumulation. This approach is particularly important for large or challenging grinding tasks.
Addressing overheating problems in grinding requires a comprehensive approach involving proper equipment setup, suitable grinding parameters, and regular maintenance practices. Operators should monitor and control heat generation during the grinding process to ensure optimal performance, extended tool life, and high-quality results.
Vibration Concerns
Excessive vibration during grinding operations can lead to various issues, including reduced surface quality, increased tool wear, and potential damage to the grinding machine. Addressing vibration concerns is crucial for achieving precise and efficient grinding processes. Here are potential causes and solutions to mitigate vibration problems:
Uneven Wheel Wear:
Cause: Irregular wear on the grinding wheel can result in uneven contact with the workpiece, causing vibrations.
Solution: Regularly inspect and dress the grinding wheel to maintain a consistent and flat surface. Proper wheel maintenance helps minimize vibrations.
Imbalanced Grinding Wheel:
Cause: An imbalance in the grinding wheel, whether due to uneven wear or manufacturing defects, can lead to vibration.
Solution: Balance the grinding wheel using a wheel balancer. Balancing ensures even distribution of weight and reduces vibrations during operation.
Inadequate Machine Calibration:
Cause: Poor calibration or misalignment of machine components, such as the wheel spindle or worktable, can contribute to vibrations.
Solution: Regularly calibrate and align machine components to ensure proper functionality. Follow the manufacturer's guidelines for machine setup and alignment.
Workpiece Imbalance:
Cause: An uneven or improperly secured workpiece can create imbalance and induce vibrations.
Solution: Secure the workpiece properly, ensuring it is evenly positioned and clamped. Address any imbalance issues before initiating the grinding process.
Incorrect Wheel Selection:
Cause: Using a grinding wheel with inappropriate specifications can result in vibrations.
Solution: Select a grinding wheel with the correct abrasive type, grit size, and bond for the material being ground. Matching the wheel to the application minimizes vibrations.
Machine Wear and Tear:
Cause: Worn-out or damaged machine components, such as bearings or spindles, can contribute to vibrations.
Solution: Regularly inspect and replace worn machine parts. Proper maintenance helps prevent excessive vibrations and extends the life of the grinding machine.
Inadequate Coolant Flow:
Cause: Insufficient coolant flow to the grinding zone can result in heat buildup and vibrations.
Solution: Optimize the coolant delivery system to ensure proper cooling. Effective cooling reduces the risk of thermal expansion and contraction, which can lead to vibrations.
Tool Holder Issues:
Cause: Problems with the tool holder or spindle interface can introduce vibrations.
Solution: Ensure the tool holder is securely mounted and properly aligned with the spindle. Use high-quality and properly maintained tool holders to minimize vibrations.
Machine Foundation:
Cause: Poor machine foundation or inadequate support can amplify vibrations.
Solution: Ensure the grinding machine is installed on a stable and properly designed foundation. Address any structural issues to minimize vibrations transmitted to the machine.
Effectively addressing vibration concerns in grinding requires a combination of proper machine maintenance, wheel selection, and workpiece handling. Operators should implement regular inspection and maintenance practices to identify and resolve issues promptly, resulting in improved grinding performance and quality.
Loading Issues in Grinding
Loading in grinding refers to the phenomenon where the spaces between abrasive grains on the grinding wheel become filled with material being ground, resulting in reduced cutting action and increased friction. Loading can negatively impact the efficiency and quality of the grinding process. Here are potential causes and solutions to address loading issues:
Soft Workpiece Material:
Cause: Grinding soft materials can lead to the rapid clogging of abrasive grains.
Solution: Use a grinding wheel with a coarser grit and open structure when working on softer materials. This helps prevent quick loading and allows for efficient chip removal.
Material Contamination:
Cause: Contaminants present in the workpiece material, such as oils, grease, or coolant residues, can contribute to loading.
Solution: Ensure proper cleaning of the workpiece before grinding to remove contaminants. Use appropriate cutting fluids or coolants to minimize loading.
Incorrect Coolant Application:
Cause: Inadequate or improper application of coolant can lead to insufficient lubrication and cooling, resulting in loading.
Solution: Optimize the coolant flow and concentration. Ensure the coolant effectively reaches the grinding zone to lubricate and cool the process, preventing loading.
Insufficient Wheel Sharpness:
Cause: Dull or worn-out grinding wheels are more prone to loading as they lose their cutting efficiency.
Solution: Regularly dress and sharpen the grinding wheel to maintain its sharpness. Use a wheel dresser to expose fresh abrasive grains and enhance cutting action.
Low Wheel Speed:
Cause: Operating the grinding wheel at a low speed may not provide enough centrifugal force to eject chips, leading to loading.
Solution: Ensure the grinding machine operates at the recommended speed for the specific wheel and workpiece combination. Higher speeds can help in better chip removal.
Excessive Pressure:
Cause: Applying too much pressure during grinding can force the material into the wheel, causing loading.
Solution: Use moderate and consistent grinding pressure. Adjust the feed rate to allow the wheel to cut efficiently without excessive pressure that leads to loading.
Wrong Wheel Specifications:
Cause: Using a grinding wheel with incorrect specifications for the material being ground can result in loading.
Solution: Select a grinding wheel with the appropriate abrasive type, grit size, and bond for the specific application. Matching the wheel to the material helps prevent loading.
Inadequate Coolant Cleaning:
Cause: Contaminated or old coolant may contribute to loading issues.
Solution: Regularly clean and replace coolant to prevent the buildup of contaminants. Fresh and clean coolant enhances lubrication and cooling, reducing the likelihood of loading.
Improper Dressing Technique:
Cause: Incorrect dressing of the grinding wheel can lead to irregularities and loading.
Solution: Dress the wheel properly using the appropriate dressing tool. Ensure that the wheel profile is consistent and free from irregularities to prevent loading.
Effectively addressing loading issues involves a combination of proper wheel selection, machine setup, and maintenance practices. Operators should follow recommended procedures, use suitable grinding parameters, and implement regular wheel dressing to minimize loading and optimize grinding performance.
Choosing the right grinding disc is crucial for achieving optimal results in various metalworking and fabrication applications. The selection depends on factors such as the material being worked on, the desired finish, and the type of grinder being used.
Choosing the Right Grinding Disc
Material Compatibility:
Ferrous Metals (Steel, Iron): Use grinding discs specifically designed for ferrous metals. These discs often contain abrasives suitable for the hardness of steel and are less prone to loading.
Non-Ferrous Metals (Aluminum, Brass): Choose discs with abrasives suitable for softer metals to prevent clogging. Aluminum oxide or silicon carbide discs are common choices.
Abrasive Material:
Aluminum Oxide: Suitable for general-purpose grinding on ferrous metals. It is durable and versatile.
Zirconia Alumina: Offers higher cutting efficiency and longevity, making it suitable for aggressive grinding on ferrous and non-ferrous metals.
Silicon Carbide: Ideal for grinding non-ferrous metals and stone. It is sharper but less durable than aluminum oxide.
Grit Size:
Coarse Grit (24-36): Rapid stock removal and heavy-duty grinding.
Medium Grit (40-60): Balances stock removal and surface finish.
Fine Grit (80-120): Provides a smooth finish, suitable for surface preparation and light grinding.
Wheel Type:
Type 27 (Depressed Center): Standard grinding disc with a flat surface, ideal for surface grinding and edge work.
Type 29 (Conical): Angled design for aggressive stock removal and better surface blending.
Type 1 (Straight): Used for cut-off applications. It provides a thin profile for accurate cutting.
Application:
Grinding: Standard grinding discs for material removal and shaping.
Cutting: Use cut-off wheels for cutting through metal, providing a straight and clean edge.
Flap Discs: Combine grinding and finishing in one. Suitable for blending and smoothing surfaces.
Compatibility with Grinder:
Ensure that the grinding disc is compatible with the type and speed of the grinder being used. Check the manufacturer's recommendations for the maximum RPM (Revolutions Per Minute) of the disc.
Task Specificity:
Heavy Stock Removal: Choose a coarse grit and a type 27 or type 29 disc for efficient material removal.
Surface Finishing: Opt for medium to fine grits with flap discs for smoother finishes.
Safety Considerations:
Follow safety guidelines, including wearing appropriate personal protective equipment (PPE) such as safety glasses and gloves.
Choose reinforced discs for added durability and safety.
Brand and Quality:
Select discs from reputable brands known for quality and consistency. High-quality discs offer better performance and durability.
Cost Consideration:
Balance the initial cost with the expected lifespan and performance of the grinding disc. High-quality discs may have a higher upfront cost but can provide better value over time.
By considering these factors, operators can choose the right grinding disc for their specific applications, ensuring efficiency, safety, and optimal results.
Conclusion
In conclusion, selecting the appropriate grinding disc is a critical aspect of achieving successful metalworking and fabrication outcomes. The choice depends on various factors such as the material being worked on, the desired finish, and the type of grinder in use. By considering material compatibility, abrasive type, grit size, wheel type, application, grinder compatibility, task specificity, safety, brand quality, and cost, operators can make informed decisions to enhance efficiency and safety in their grinding processes.
It's essential to adhere to safety guidelines, wear appropriate personal protective equipment, and follow manufacturer recommendations for grinder and disc compatibility. Whether it's for heavy stock removal, surface finishing, or cutting applications, the right grinding disc can significantly impact the quality and efficiency of the work.
Additionally, periodic checks for wear and tear, addressing issues like overheating and vibration concerns, and understanding loading problems contribute to prolonging the life of the grinding disc and ensuring consistent performance.
In summary, a well-informed and systematic approach to selecting, using, and maintaining grinding discs is key to achieving optimal results, enhancing productivity, and ensuring a safe working environment.
Post time: Jan-12-2024